Europe’s most value-adding and accessible EMS manufacturer
Latest News
Let us help you accomplish more
With more than 60 years of experience in the field of Electronics Manufacturing Services (EMS) and with a truly global setup, we are ready to help you accomplish more; no matter your location, your needs, or your challenges.
Our unique customer-centric approach is your biggest advantage. We offer access to leading experts on all levels. And with a dedicated servant approach, we can help with everything from research, development and innovation to daily operations and strategic sparring. Explore our services and approach to learn how we can add value to you and to your business.
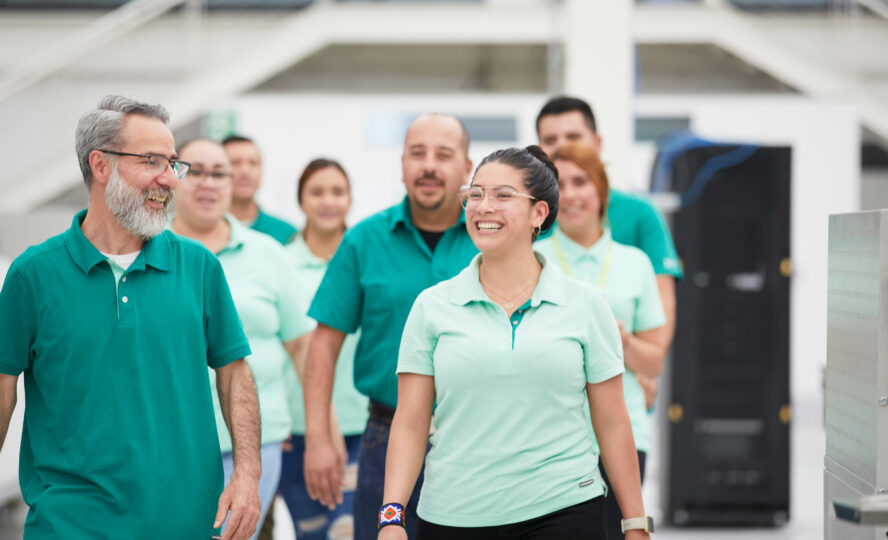
Global – and uniquely local
We operate at a truly global scale, but we know proximity is king. To us, closeness is about more than just geographical closeness. It is about matching mindsets and likeminded ambitions. Answers to your challenges and needs. Every time.

Do more with less
Want to know more about our role as a responsible EMS partner?
Sustainability

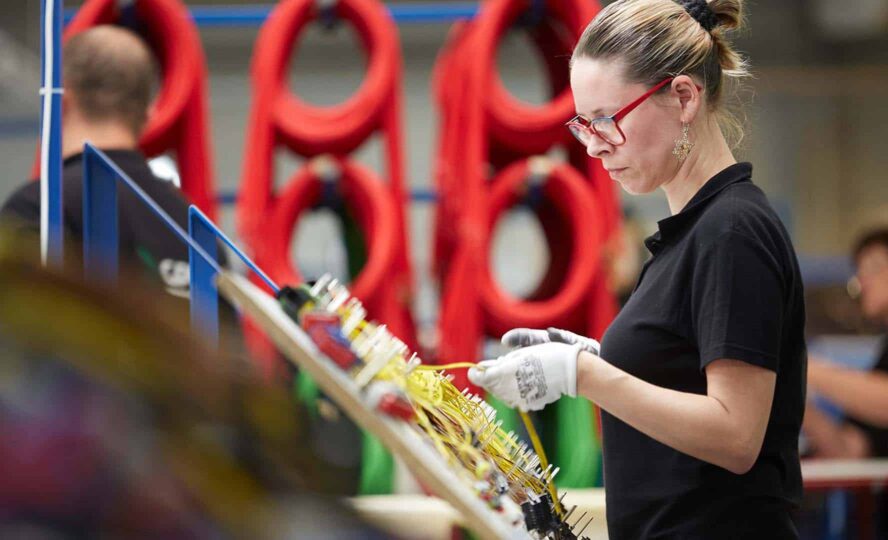




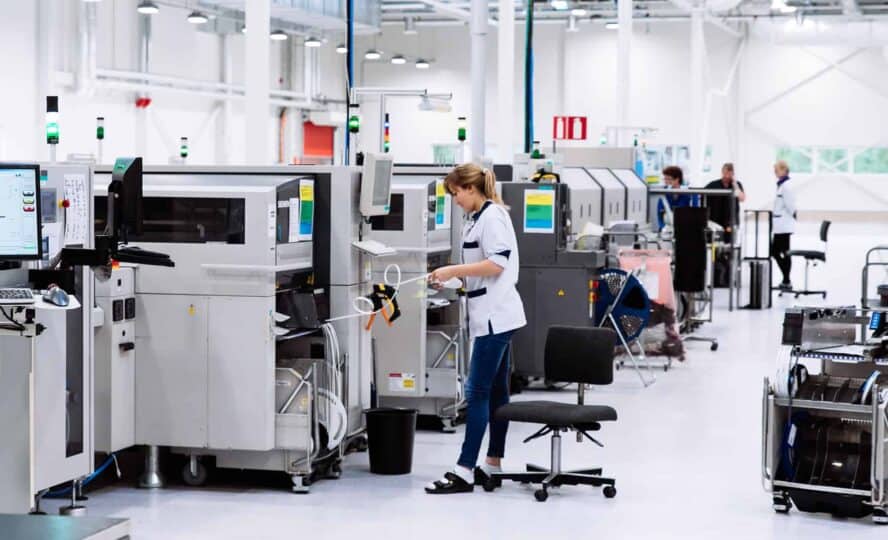

Ambitions are useless without people
Meet some of our dedicated people from our locations all over the world.